With the winter holidays approaching, Amazon and Walmart are touting the recent improvements in speed and efficiency seen due to shifts in their fulfillment strategies.
This holiday season will mark the first one that Walmart customers will begin feeling the benefits of the retailer’s “next generation supply chain,” the company announced this week.
Walmart already has three next-generation fulfillment centers open in Joliet, Illinois; McCordsville, Indiana; and Lancaster, Texas. A fourth is expected to open next year in Greencastle, Pennsylvania. Last month, Walmart unveiled plans for its fifth next generation fulfillment center with a 900,000-square-foot facility in Stockton, California, slated to start operations in 2026.
Earlier this year Amazon completed its shift from a single national fulfillment center in the U.S. to eight distinct regions in a bid to slash costs and optimize delivery speeds.
Amazon’s shift to a regional fulfillment network exceeded the company’s expectations, making “more impact than we optimistically expected,” President and CEO Andy Jassy said during a recent Q3 earnings call.
Here’s what the companies shared recently about how their fulfillment pivots are faring.
Walmart zeroes in on convenience, availability and accuracy
With the three next generation facilities that are currently operational, Walmart has been able to “drastically increase” its number of orders for next-day shipping, David Guggina, Jennifer McKeehan and Parvez Musani, three Walmart supply chain, delivery and fulfillment executives, said in a recent company blog post.
Totaling approximately 1.5 million square feet, the three centers have a larger assortment of popular items including clothing, toys, electronics and more.
The retailer is expanding automated technology in its distribution centers to make deliveries to stores faster and more efficient, noting that more than 15% of its stores this year will receive merchandise from automated distribution centers.
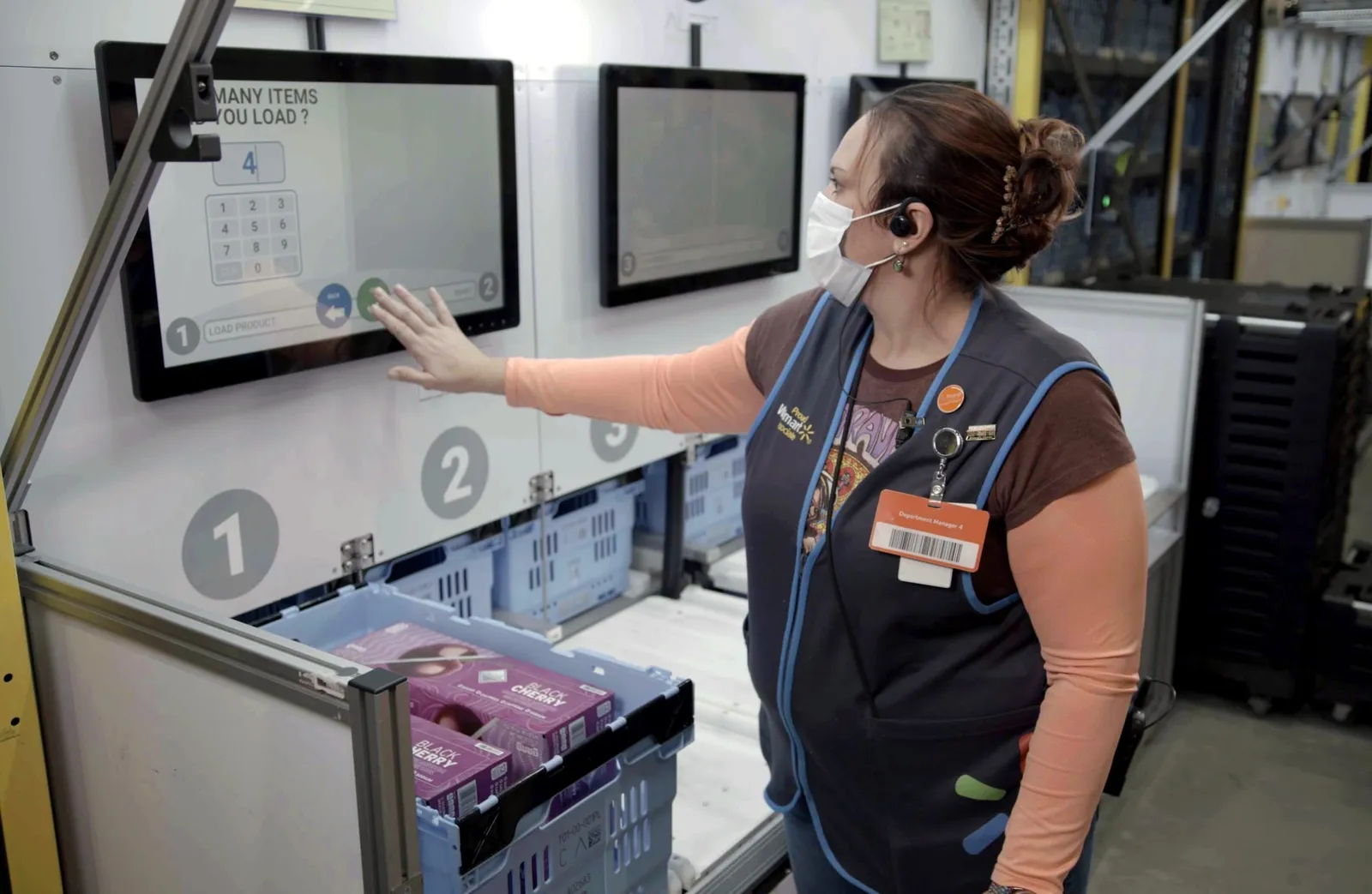
Along with the next generation facilities, Walmart also said it will have seven automated market fulfillment centers, which are located within the retailer’s stores, operating by Thanksgiving. Stocking “thousands of the most sought-after items,” these centers will have inventory that is distinct from the sales floors of the stores with a focus instead on assortment needs specifically for pickup and delivery order fulfillment, the blog post noted.
“This approach both ensures heightened accuracy and also minimizes the need for substitutions, offering our customers an even more precise and satisfying shopping experience,” the executives said in the blog.
The blog post also noted that Walmart has expanded its same-day delivery hours again. In September, the retailer revealed it would let customers who order by 9:30 p.m. get their orders delivered same-day by 10 p.m. This holiday season, customers can use Late Night Delivery services until 10:30 p.m. across 4,000 stores.
With the fulfillment and delivery updates, Walmart is banking on its staffing to keep its delivery promises.
Walmart wants to have its employees handle more last-mile deliveries, President and CEO Doug McMillon said at the Goldman Sachs Global Retailing Conference in September.
Amazon’s fulfillment network shift exceeds expectations
Amazon has sought to right-size its national fulfillment network over the past year after the initial pandemic-driven spike in e-commerce demand leveled off.
Previously, Amazon had to ship a product from across the country if a local center didn’t have the item in stock, which lengthened delivery times. With the shift to the regional strategy, the benefits come in many forms, including higher stock levels and improved connectivity between different facilities and delivery stations, resulting in shorter delivery routes and faster delivery speeds, Jassy told analysts.
“We continue to make steady improvements in fine-tuning the placement algorithms to enable even more in-region fulfillment and to further increase consolidation into fewer shipments,” Jassy said.
While Amazon is no longer zeroed in on rapidly growing its operational capacity with new real estate, its goal to boost shipping speeds remains the same.
“Shorter travel distances and fewer touches mean lower cost to serve,” Jassy said. “But perhaps most importantly, shorter distances and fewer touches mean that customers are getting their shipments faster. We remain on pace to deliver the fastest delivery speeds for Prime customers in our 29-year history.”
Amazon has continued to slow down its fulfillment spend and reduce fulfillment complexity and cost, and is focusing on other ways to streamline its operations and boost delivery speed for Prime members.
The push includes optimizing inventory stock levels in the company’s regional network using placement algorithms, which is helping drive cost cuts, the CEO said. Jassy also noted that Amazon shifted many of its fulfillment and sortation center connections to instead be more direct connections between fulfillment centers and delivery stations, which is “easier to do when you have more local in-stock in a region.”