In this fast-paced industry where customers are looking for the fastest delivery and using multiple channels to complete their purchases, brands need to stay ahead. Today, almost all consumers check reviews and compare prices both online and offline before making a purchase.
Continuous market uncertainties mean complex demand anticipation and needing to have products available for customers whenever they desire. This has led to the growth of the omnichannel market. Omnichannel is the new normal as consumers can shop from any
channel they desire for easy availability.
The accelerated growth of the changes in the supply chain and rise in demand has pushed the need for automation and reduced the dependency on human capital alone.
To remain competitive, manufacturing and ecommerce companies are considering larger investments in advanced technologies to ramp up their warehouse and logistics operations for a smooth omnichannel experience for their customers.
Why is it essential to consider automation?
From adding order details to delivering product to a customer, conventional warehouses cannot meet the requirement of omnichannel operations. Why? There are many important factors that can disrupt the supply chain and create a poor customer experience.
Automation in omnichannel processes can help:
- Avoid the rising cost of warehouse space
- Manage the varieties of orders and SKUs
- Create timely and accurate order fulfilment to stores and customers
- Increase safety by reducing warehouse traffic
- Boost productivity with faster workflow – picking, packing and transporting
- Manage the seasonal and peak month fluctuations
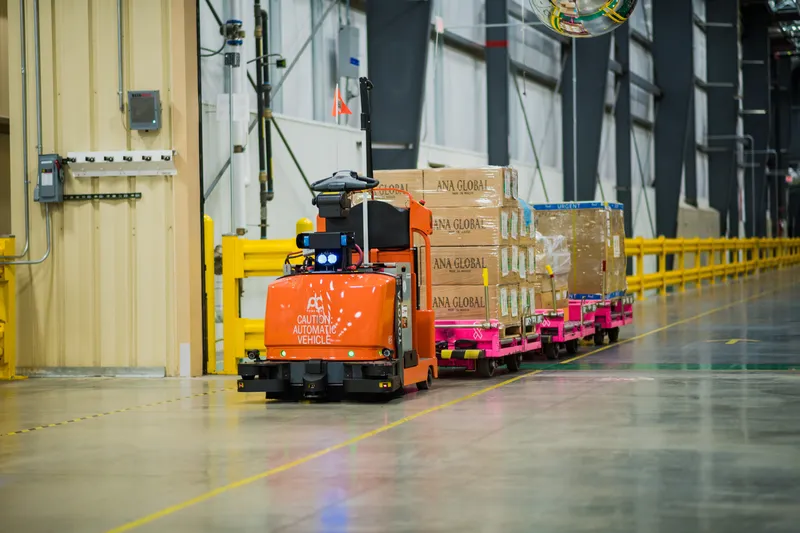
Automation for resilient operations
There is no doubt that the market is evolving rapidly, connected with consumer demand for free shipping and same-day deliveries. The need for automation is also steadily growing.
Technology advancements can re-engineer the traditional warehouse and distribution centers for more resilient and efficient operations. Companies must navigate their choices and expectation to make their omnichannel warehouses resilient, dependable and responsive to quickly adapt to the market requirement.
Some points of consideration when reviewing various automation options include:
- ASRS (automated storage and retrieval systems) for the maximum case, tote, and pallet storage in bulk and space optimization
- Palletizing robots to ease put-away from dock to rack
- Picking robots for case picking and small unit item picking from shelves and bins
- AVs (Autonomous Vehicles) to transport cases, pallets, or bins to dedicated shelves or replenishment locations
- Integrated supply chain software or warehouse control systems to facilitate the processes and real-time inventory visibility
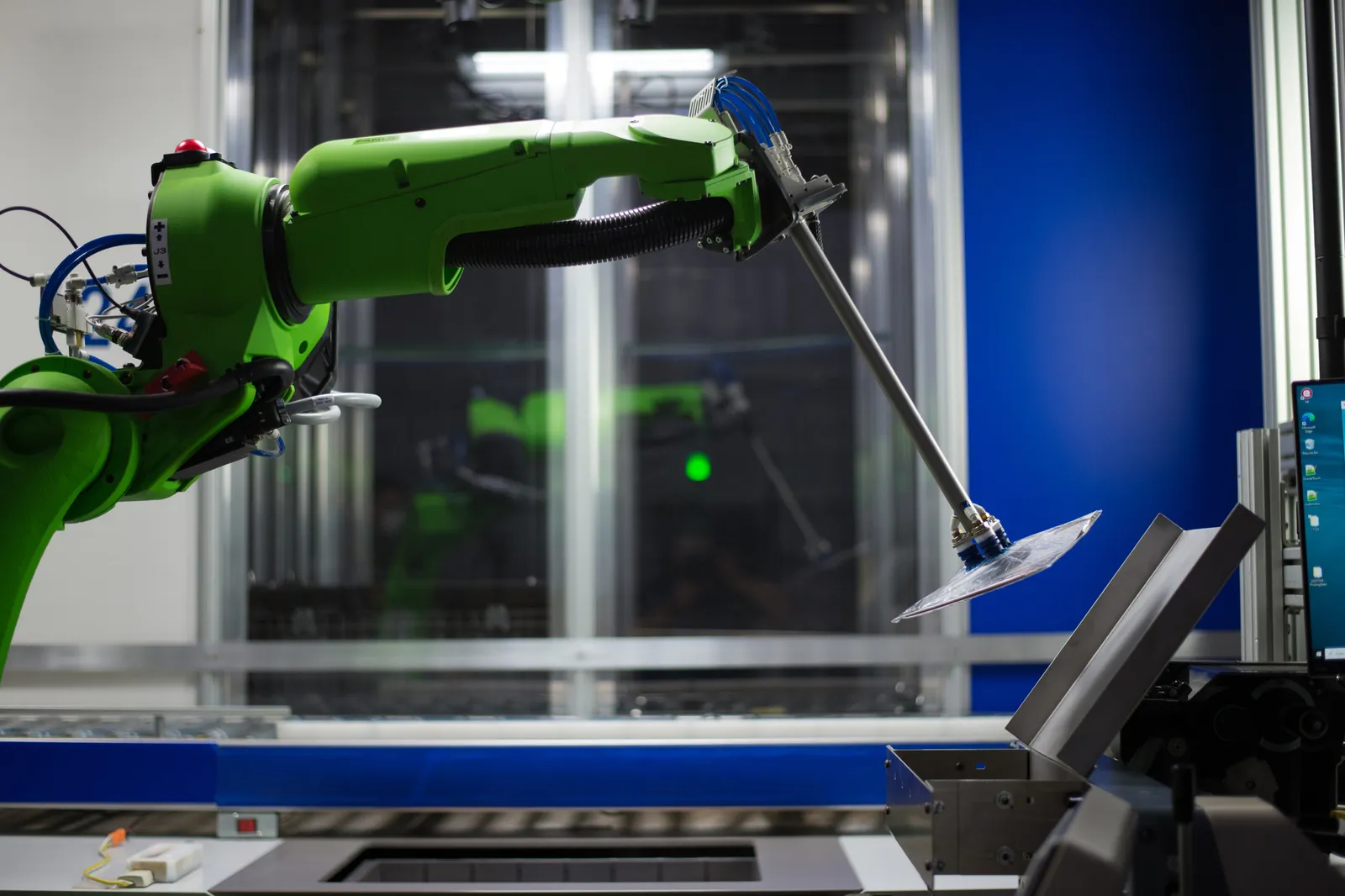
Choose the right integrator
Omnichannel logistics gives consumers a unified experience across all touchpoints- product availability, delivery to return options. Companies that can innovate to deliver a great customer experience with personalized services can keep their pace in the market. The
combination of required material handling equipment can smoothen the operations of order fulfilment and product handling. There are numerous other things that can be done to make the warehouse fully automated, but businesses must plan in advance to ensure maximum benefits.
It is most beneficial to have an efficient material handling and advanced automation partner who will help create a seamless omnichannel distribution center to equip with a rapidly changing market.
Whether in the United States, India, Brazil, Mexico or Canada, our experts can guide you to understand the technologies that will optimize your omnichannel operations. The team will examine your operations and data thoroughly from order cycle times, equipment interface, and SKUs to delivery routes, so that they can help identify the best technologies to support you for higher throughputs, streamlined workflows, accurate order picking, and improved service.